Operations Improvement & the Most Productive Day of the Week
- Arend Pryor
- Dec 21, 2021
- 6 min read
Updated: Jan 3, 2022
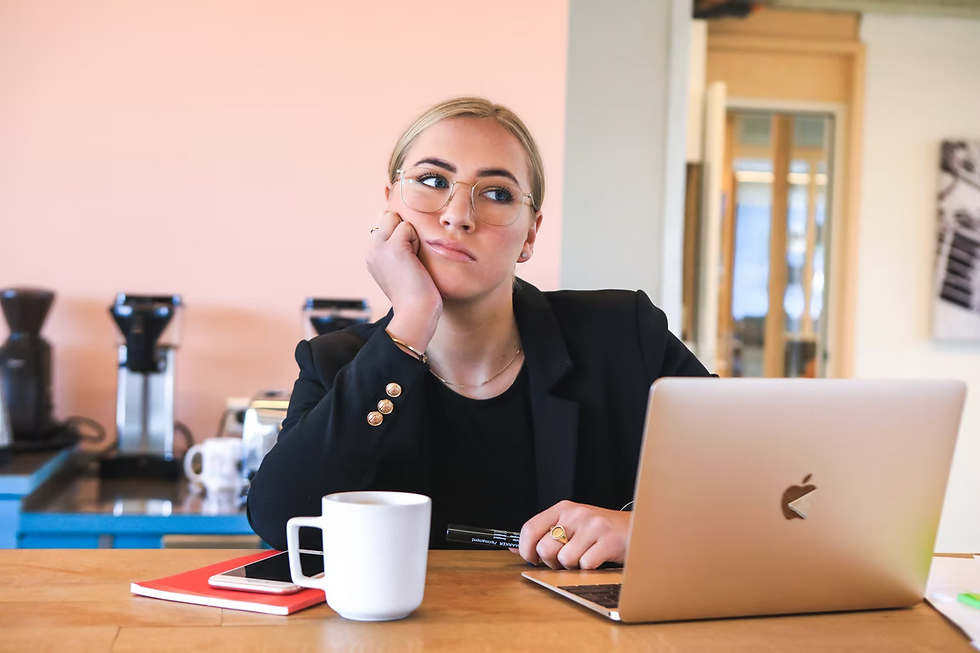
Author: Arend Pryor | Published: 05/06/2021
Details: Sharing content created as part of pursuing my MBA degree
Assignment: Write a response to the following in a minimum of 500 words:
Describe an example where Theory of Constraints (TOC) was successfully applied to improve a process, or where you saw the potential for TOC to improve the process, in either a company you worked for or a company you were a customer at.
What is the Lean concept and why is it important to study? How can Lean be applied to manufacturing and service processes?
What is work center scheduling and why is it important for firms to focus on?
According to a study by the accounting and financial staffing firm Accountemps, the day of the week employees feel most productive and committed is Tuesday (Li, 2020). With Friday being the least productive day of the week, it stands to reason that it could be considered the bottleneck of days. Finding ways of improving processes and efficiency at work, is the name of the game for many who find themselves in a managerial role. This often starts with using an approach called the Theory of Constraints, which focuses primarily on finding the bottleneck within a system and working to improve its flow rate, which will result in improving the overall process (Cachon & Terwiesch, 2019). Another concept that is commonly used and studied by many in the manufacturing and service industry is the Lean approach. This system was popularized as a result of research done by management scholar James Womack and his study of the Toyota Production System. A certification and study of these concepts can provide companies with a competitive advantage by simply eliminating wasted efforts, energy, and/or steps from their processes. On the work center scheduling side of things, it is important for those in charge to have a good grasp of this concept and the many approaches available when it comes to maximizing the utilization of their resources.

A few years back I got into the world of online teaching and made my first course on using a graphic design program called Sketch. The goal of the course was to teach beginners the basics of the program and then walk them through the process of recreating a variety of real-world designs to give them hands on experience with the program. The process involved with making each section of the course flowed really well, except for when it came time to actually record the videos. There were a good deal of stops and starts, issues with remembering what to say, and at times, getting off track.
Based on the theory of constraints, the flow rate of a process can often be determined by the flow rate achieved through the bottleneck that exists within the entire process (Cachon & Terwiesch, 2019). Taking this into consideration, the recording phase seemed to be my bottleneck as it limited the number of videos I was able to create, edit, and post per week.

Identifying a constraint is generally the first step and will often come as a result of analyzing a process and asking what it is that’s preventing you from making or selling more items (Examples of Constraints, 2020). This is step one in the Five Focusing Steps, which looks to find the constraint and work to eliminate it from the process (Vorne, 2019). Despite not being familiar with these steps, they very closely align with the process I followed to eliminate the constraint. By focusing more effort up front and creating a script for recording rather than just having a few bullet points to follow, my recording issues all but disappeared.
When I think of the term lean, it generates thoughts of mixed martial arts fighters who have successfully cut weight and find themselves standing on a scale weighing in with zero percent body fat. In a way, this process is very similar to the lean concepts applied by many companies. Both have a goal of removing waste from their system in an effort to improve and perform at a more efficient level. From a company perspective, removing waste is done by analyzing the resources and flow units within a system and identifying opportunities to eliminate wasted time, energy, and efforts.
This can apply to people as well as machines or both (Cachon & Terwiesch, 2019). The study of Lean concepts can offer many benefits to organizations regardless of their industry, but more importantly, these concepts can help prevent issues such as overproduction, storing too much inventory, resources sitting idle, or duplication of efforts (Ciraldo, 2021). In order to prevent these issues and reduce waste, companies typically analyze their manufacturing or service processes to identify one of the following seven types of waste:
Waiting: Workers who spend too much time waiting for inputs from the prior step or standing around waiting for a machine to complete a process.
Overproduction: Creating a number of items that exceed the demand for those items
Inventory: Gathering too much inventory can lead to subsequent waste such as storage space, additional inventory handling, and transportation of that inventory.
Transport: Moving items from one location to another
Excessive Processing or Incorrect Processing: Spending too much time working on a flow unit or incorrectly working on it
Rework: The process of having to repeat a process due to an error
Unnecessary Motions and Movements: This one speaks for itself, but in short, this deals with determining the most efficient way of performing a particular task (or tasks) and executing the process so as to limit wasted motions and movements (Cachon & Terwiesch, 2019)
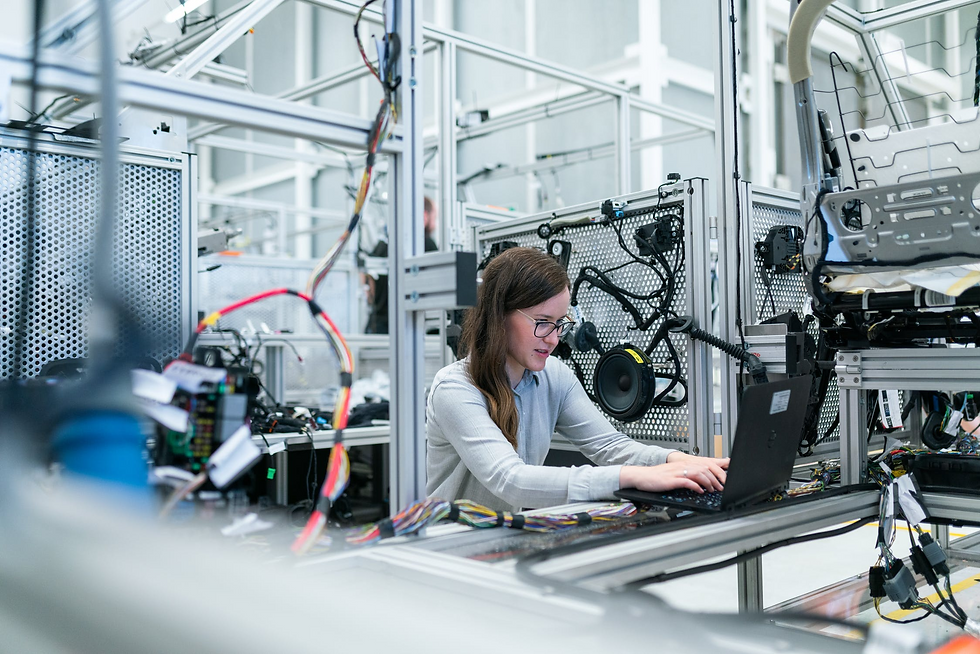
Lastly, let’s cover work centers and scheduling. A work center is a physical or logical processing area or location, while scheduling determines how the resources in these areas are used or organized to carry out various operations (What Is Work Center?, 2021). Diving a bit further down the rabbit hole, scheduling is the roadmap that allows companies to accomplish long or short term goals, produce a new product, execute a contract, or perform a service.
Regardless of the timeframe that these items occur, short term, midterm, or years in the future, scheduling the details establishes a plan of action and helps organize the resources and activities involved as well as help in monitoring progress along the way. Finding the best method of scheduling the time spent by company resources is also important as this will help maximize flow times, via the way jobs are processed. For example, using a First Come First Served (FCFS) method versus Shortest Processing Time (SPT), each of which have their own benefits. For instance, the FCFS method can be a good choice when there are a very small number of jobs in the queue, while SPT can be the optimal choice when a larger number of jobs need to be processed. In the ladder situation, demand would be higher as would capacity, which would favor using SPT (Cachon & Terwiesch, 2019). Unfortunately, the decision is not always this easy. When you add in factors such as multiple resources, priority, and the weight each job places on your system, the complexity of the decision can quickly increase. You can see that being familiar with the tools and concepts of scheduling are important ones to master and focus on as they each have an impact on your company’s ability to efficiently meet the demand of your customers or even the decision to expand.
While you may not be ready to show up on Monday morning ready to turn your company’s weaknesses into strengths, you will no doubt be more inclined to start implementing the approaches talked about above on Tuesday. As seen above, starting with the Theory of Constraints, we know the importance of identifying the bottleneck in the process and taking steps to improve its overall throughput, which will result in increased flow times in your system. Starting on Wednesday, we can show up to work with a well-rounded knowledge of Lean concepts and apply them to the manufacturing and service processes used by our company in an effort to eliminate waste. A practice that not only aims to better service the customer, but provide a competitive advantage within your industry. Lastly, we come to Thursday and your opportunity to implement what you know about the topic of work-center scheduling. This is your moment to shine when you analyze the current scheduling practices used by your company and perform an analysis of the best approach to take in scheduling resources. Having familiarity with elements such as multiple resources, priorities, and job weights can aid in choosing an optimal scheduling method. While you might not be able to accomplish all of this in a single week, scheduling time to get acquainted with these concepts and approaches over a period of time, will no doubt include taking back Friday’s making them productive once again.
References
Cachon, G., & Terwiesch, C. (2019). Operations Management 2nd Edition, International
Student Edition. (2nd ed.). McGraw-Hill Education.
Ciraldo, J. (2021). What Is Lean Operations and How Can I Use It to Save Money?
Retrieved from https://www.beekeeper.io/blog/lean-operations/
Examples of constraints. (2020). Theory of Constraints Institute.
Li, L. (2020). 7 Surprising Facts about Employee Productivity. TINYpulse.
Vorne. (2019). Focus improvement on the manufacturing constraint | lean
production. LeanProduction. https://www.leanproduction.com/theory-of-
What is work center? (2021, April 16). ERP Information.
Comments